Once the master hull, superstructures, boats, etc., have
been crafted, several decisions must be made regarding how complete the
sub-masters are to be before the mold is made. Here we find two primary
approaches. The Germans have developed a very advanced method of casting
wherein nearly the entire model, down to 20 mm guns, is cast as a single
unit (minus main turrets, cranes, and top-masts). This has the great advantage
of eliminating many assembly steps, which saves a lot of money and time.
Such an approach may result in a certain number of casting failures, but
this is no problem because the metal used can be melted down and cast again.
The main disadvantage of this approach is that painting the models in
complex schemes is very difficult because many tiny nooks and crannies
must be worked around. Thus, the gray monochromatic sprayed-on look we've
all come to know. Some of us have grown to accept and like this look. However,
many collectors are now asking for realistically painted decks and the
like, and this drives up the production costs because the detailed painting
of a nearly complete casting is no easy task! It is time consuming
and expensive – although the end-results are very impressive.
Dave has taken another approach. He is making castings that are devoid
of many detail parts so that the models may be easily painted. Once painted,
the detail parts can be added, and thus there is no need to work around
tiny AA guns and the like. The reason this approach is being taken is because
Dave plans on using two rather complex paint schemes. One involves an overall
British gray, but with painted main and upper decks -- as well as many
other details. The other theme is a very complicated multi-color camouflage
pattern as worn by some KGV class ships during the mid-war period. Here
we find a general approach wherein it is hoped the time saved in painting
will offset the time employed in assembly. I have no idea if this will
work out, but the process will also allow us to market the detail parts
many of you have requested. Pictured below are the actual castings Dave
has gotten from the molds.
Making these castings involves the creation of a complex silicone mold
that is composed of a number of elements that fit together like a 3D puzzle.
The exact way this is done varies from producer to producer, and many model
makers keep the details very close to the vest.
Basically, the mold-making material is placed around a sub-master that
is embedded within in a block-shaped form. In many cases, silicone wedges
are used to orient the model within the form, and pouring vents are also
worked into the pattern. The silicone cures, and the sub-master is removed
from the form via a number of mechanisms that have been worked into the
form’s structure. For example, some molds have male and female interlocked
halves that run amidships as primary components, and once the mold cures,
the sub-master is carefully removed from the mold halves via a number of
small dentist-type tools. Of course, modern molds can have subcomponents
worked into them around various structures, such as tripod masts, but that
methodology’s workings are not widely shared. Moreover, there are many
types of hard and soft silicone, and this is not the only material that
can be used to make molds.
Dave will present pictures of how he makes molds, but as I explained
-- most model makers are reluctant about sharing details of this process
-- which is the end result of a lot of hard work and experimentation.
For Dave's approach to work, each casting must be crisp and sharp and
involve a minimum of cleaning up. All castings require the waterline area
to be filed or sanded to be flat, but incursions of material into the deck
and other areas are to be avoided at all costs. In addition, the bulwarks
must not have holes, which is no easy task because they are very thin structures.
Lastly, Dave is employing an expensive slow-cure resin, so there is no
room for error. If a casting is not right -- it must be thrown away because
it cannot be melted down and remade.
The type of casting material used is very important because shrinkage
is a major factor if subcomponents such as turrets are to fit properly.
Our German friends have this down to a science with regard to the use of
metal alloys, but the resin casters have also made great progress. Dave's
selected material has very little if any shrinkage, and thus the turrets
fit well, even though the clearances were tiny in the master.
|
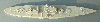 |
The use of extreme magnification is a must because this
will show all of a casting's warts and what needs to be cleaned up. It
seems the hatches and deck equipment are OK. These photographs have been
magnified by a factor of about 7 or so. It is hard to get clear closeups
with a camera, and thus the Mk 1 eyeball is important here.
At one time resin used to form bubbles during the curing process which
made holes, but the newer types of resin do not do this very much. Still,
all parts of the casting must be checked under extreme magnification. The
shot of the forward turrets is as close as the camera can get -- and is
fairly close to a magnification factor of 9 or so. We are looking for pitting,
sharpness, grain structure, etc., and we do this for the entire model. |